Description
A fully functional melting unit and roller application system are of major importance for a smooth and reproducible adhesive application. The cleaning effort varies depending on the application system and unit, and depends largely on the type of adhesive used. It is recommended that the application system be cleaned before any downtimes and adhesive changes, and Jowat supplies a range of flushing agents and cleaners for that Purpose.


Melter and Hoses
Jowat® flushing agents purge the adhesive and stop the chemical reaction of PUR hot melt adhesives. Before the cleaning of the application system is started, it must be ensured that the Jowat® flushing agents and the adhesive used are compatible. To prevent plugged hoses or nozzles due to an unwanted reaction, especially in closed application systems, it must be ensured that the PUR hot melt adhesive and the Jowat® flushing agent are melted evenly.
The primary task of a flushing agent is to push out the adhesive from the hoses and the application unit, and therefore to purge product remnants from the system. Due to the general flow behaviour of liquids (cf. figure 1, on the right), the flow velocity is significantly lower at the walls compared to the centre of the hose. To ensure that the hoses are cleaned thoroughly, it is thus necessary to use a sufficient amount of flushing agent.
Apart from flow velocity, viscosity also plays a role in the purging process. If the viscosity of the flushing agent is too low, it will only purge the adhesive in the centre of the hose. Under those circumstances, it will not be possible to remove all the adhesive. To find out the viscosity of the flushing agent and the hot melt adhesive, please refer to the corresponding Technical Data Sheets (available upon request).
Drum Melters
Avoid any contamination during drum changes. The heating plate is to be cleaned and remnants around the sealing rings are to be removed. Greasing the sealing rings with a suitable water-free and acid-free grease (e.g. rolling bearing grease “Petamo GY 193” supplied by Klueber Lubrication) facilitates easier cleaning and thus considerably reduces the downtime during the change of the drum. The drum may not remain open longer than necessary.
Roller Application System
Standard Operation (Synchronised)
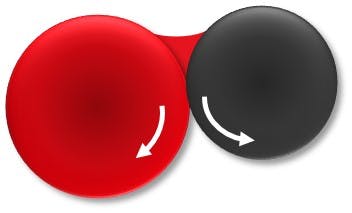
Cleaning (Reversed Direction)


Drain the roller application system using the machine’s cleaning program (reversed direction). The hot melt adhesive remnants should be collected in a coated drip pan or a similar container.

In addition, hot melt adhesive may be cleaned off the application roller using a wooden spatula. It is recommended that the roller rotation be turned off for this procedure.

Set the roller application system to standard operation mode, fill with Jowat® cleaner 930.22 (approx. 1 kg) and melt.

Allow to soak for 10 to 15 minutes while the rollers are rotating in standard operation mode.

In addition, the rollers may optionally also be cleaned using the cleaner Jowat® 930.65 (approx. 1 litre), heated, and allowed to soak for approx. 10 minutes while the rollers are rotating (standard operation mode).

Run the rollers in reverse (cleaning mode) to drain the liquid cleaner into the catch pan.
Then, set the roller application system to standard operation mode and repeat the procedure up to three times depending on the degree of soiling.
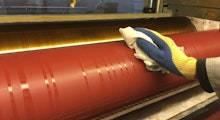
Remove all flushing agent remnants after cooling – but while still warm – by wearing protective gloves and using a dry, lintfree cloth (if necessary, slightly soaked with cleaner Jowat® 402.38). The cleaner Jowat® 930.60 can be used for soiled metal parts. Crosslinked PUR hot melt adhesive can be removed only mechanically.
Chemical Cleaning of Metal Parts
The cleaner Jowat® 930.60 detaches charred and cured adhesive from tools, nozzles, filters, and other small parts made of metal. The disassembled metal parts may be cleaned in a heated bath at approx. 180 °C (e.g. in a commercially available deep fryer). Depending on the degree of soiling, the cleaning procedure may take about 60 to 120 minutes. The temperature of the bath must not exceed 190 °C. Remove parts from the bath, allow for cooling, rinse with water, and dry. Please also observe all recommendations of the equipment manufacturer.
Seals and other plastic parts may be dissolved and may need to be replaced!
Product Information
- Flushing agents
- Cleaning agents
Flushing agents
Cleaning agents
The products listed only represent a limited selection of the available product portfolio. Product availability might differ by region. The technical data, characteristics and field of application provided in the table outline the differences between the individual adhesives of the product portfolio. Our Application Technology Department and our Sales Representatives are on hand to provide advice and support you finding the best adhesive for your particular application.
Note: The information on this page is based on test results from our laboratories as well as on experience gained in the field, and does in no way constitute any guarantee of properties. Due to the wide range of different applications, substrates, and processing methods beyond our control, no liability may be derived from these indications nor from the information provided by our free technical advisory service. Customer trials under everyday conditions, testing for suitability at normal processing conditions, and appropriate fit-for-purpose testing are absolutely necessary. For the specifications as well as further information, please refer to the latest technical data sheets.
Safety Remarks
PUR hot melt adhesives contain isocyanate groups as reactive component. Isocyanate vapours may be released at higher adhesive temperatures. Vapours that may form are to be extracted via suitable ventilation and extraction systems. For more information concerning safety, handling, transport, and disposal, please refer to the corresponding Safety Data Sheet (available upon request). The information on this manual is based on test results from our laboratories as well as on reported experience gained in the field by our customers.
It can, however, not cover all parameters for each specific application and is therefore not binding upon Jowat, nor should it be relied upon in lieu of your own required testing. The information given in this leaflet does not represent a performance guarantee. Unless otherwise agreed with our customers, the values stated in the section “Specification” shall be regarded as the product properties finally agreed. No liability may be derived from the information contained herein nor from the information provided by our free technical advisory service.